Let’s take it down to something that’s rather more simple.
A mortar
Here is a french light mortar from WWII
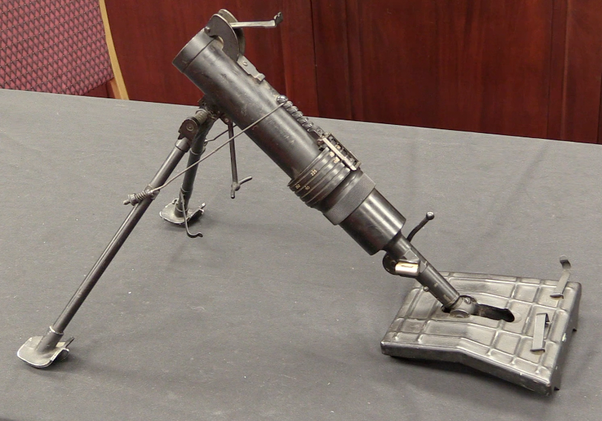
This is an incredibly simple design. Everything you need, nothing you don’t. It only weighs 8 pounds. It folds down to something that can easily fit in a small pack. It’s simple to operate: Put it at a 45 degree angle and set range with a simple screw system, and change windage (slightly) with another one.
This, frankly, is a great weapon that gives infantry indirect fire support in virtually any situation.
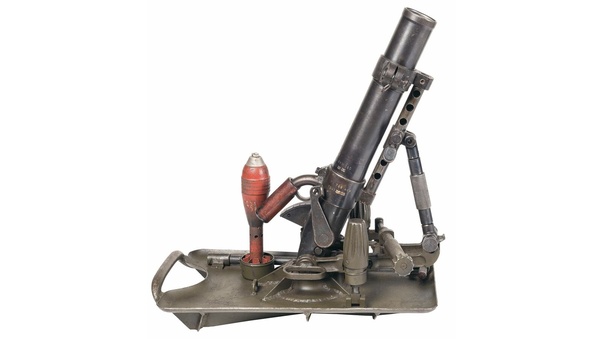
This is the equivalent German light mortar.
This is not a simple design. This thing weighs 31 pounds. It does fire a heavier projectile, but not worth it for the crazy increase of weight. It disassembles (because you really want two people to carry this), but not anywhere near as easily or quickly as the French system.
You have to level it with overly heavy and complex controls. There’s two range adjustments. They originally came with a telescopic sight system that is just excessive.
If you are going to spend 31 pounds on this thing, it makes a lot of sense to just step up to 42 pounds and get the MUCH more powerful 60mm mortar like the US M2.
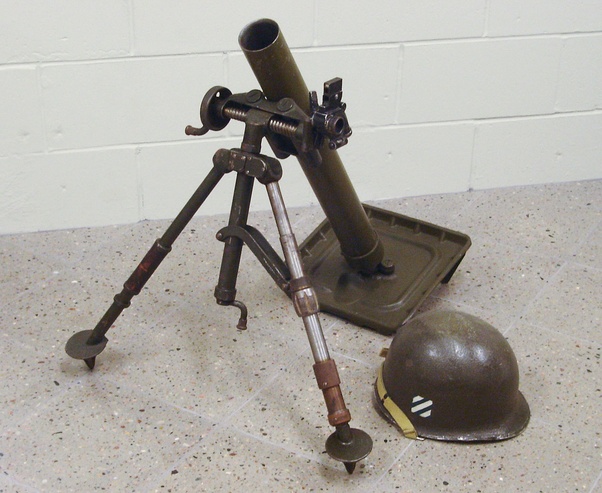
Which, bizarrely, still looks broadly simpler than the german design.
The germany system here is a classic example of over-engineering. Of worrying about things that didn’t matter, at the expense of what did matter. This sort of thing is endemic in WWII era German arms.
I’m still convinced that we should have bought this thing:
11 pounds, one man operation… And the spiritual descendent of the French system (And the Japanese “knee mortar”)
German engineers have a habit of designing systems that appeal to engineers in a laboratory environment rather than users and technicians in a field environment.
One example is in tank tracks. Most tanks have basically linear road wheels.
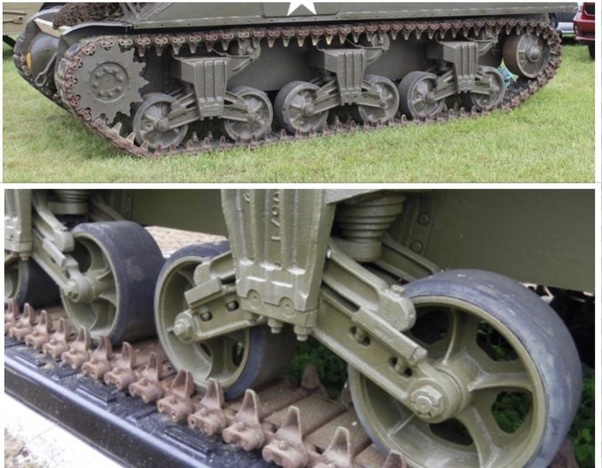
Sherman tracks
The Germans used interleaved road wheels, which provide a much smoother ride.
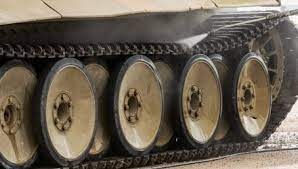
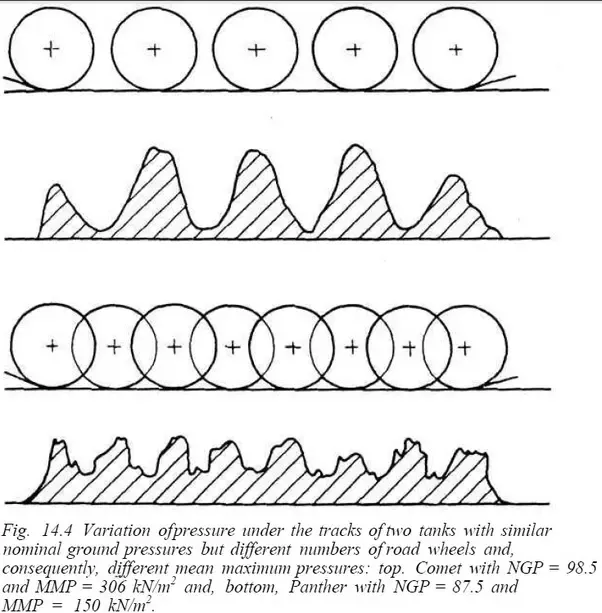
The problem is that when one of the wheels is damaged, with a conventional design you replace the wheel. With German designs, unless it’s an outer wheel, you have to take off at least three wheels to replace the damaged one.
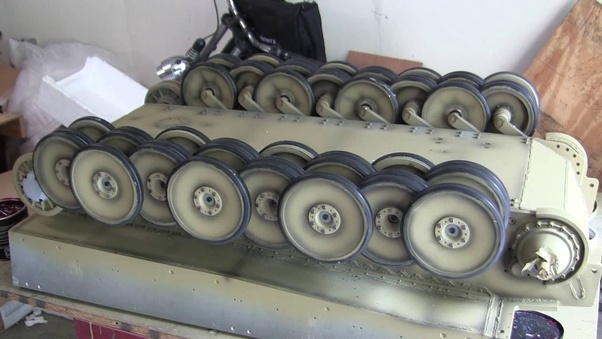
This is more work and keeps the tank down and out of combat for longer.
Another example, the Germans designed lovely and well protected transmissions for their tanks. The Sherman transmission was more exposed, but also the entire unit could be replaced in field conditions.
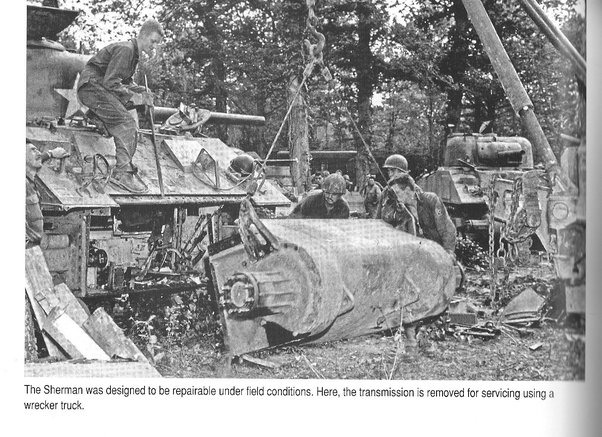
What this essentially resulted in is that German tanks were more complicated and expensive to build, which means fewer of them could be put on the field, and it took more effort, expertise, manpower, and material to keep them operating. When they worked, they worked really well. When they worked. But they spent a lot of time down and out for repairs.
American tanks, on the other hand, were built with looser tolerances, simpler systems, and on the assumption that they would be damaged and that a bunch of GIs used to fixing tractors were going to get the things up and running again, come hell or high water, and not wait for the depot mechanics to do a “proper” job of it, so they better design a tank that was field-repairable. In point of fact, the first echelon of maintenance and repair for American tanks were American tankers. The first echelon for the Germans, by the book at least, was the battalion repair depot.
Essentially, Germans tried to make everything too precise. It’s nice if your tank can shoot a dime at 2000 meters, but all it has to do is shoot another tank. And a tank that is just accurate enough to hit another tank is going to have a simpler, more robust gun system than a sniper rifle masquerading as a tank.
People argue about the use of that term. To the supposed purists, it means that that too much effort was put into design than was warranted, which is not the case.
I prefer the term “overly complex”. They chose the absolute best engineering solution to a problem, without giving enough thought to how it would be used in the field. And all aspects of the vehicle were finely made and machined.
Here is a picture of a Russian T-34.
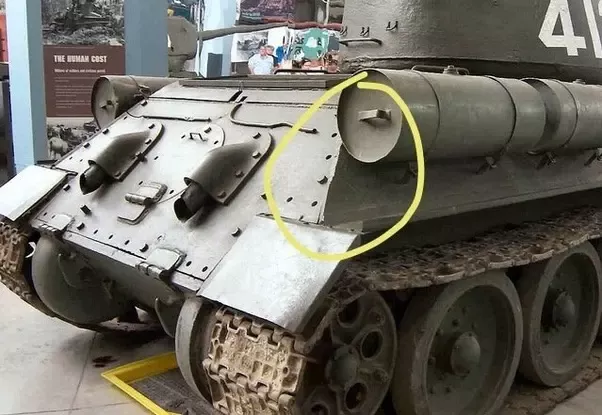
Note the bit of armor that is circled. It looks as if it was bolted on, then somebody said “oh crap, there is supposed to be a curve here”, and ground it off or cut it off with a torch. Look at the other side, where the round exterior fuel tank protrudes past the armor? On the side with the circle, the round bit wasn’t cut properly, so the tank can’t protrude. You will also notice a fair number of missing bolts. Others have said it’s because it is a museum tank, and they have been lost over the years. But in my experience, and having watched every video about the Bovington Tank Museum I can find, I doubt a serious museum would let that pass. They would scrounge from other, unrestored tanks, or if necessary, hand craft a modern replacement.
I saw it gawdawful ugly? Yes. Would a German final inspector die of a stroke on the spot if he saw that coming out of a factory? No doubt. Does it affect performance? Not in a significant way.
Here is a Sherman drawing.
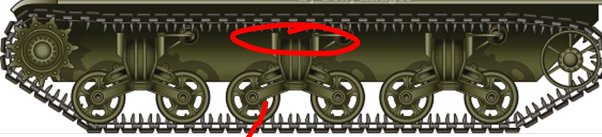
If a road wheel goes bad, at the bottom, you reduce track tension with a big wrench, and a log, and you unbolt the entire bogey (red, badly drawn oval). And you slap on another. One thing the US did very well, is stock spares assemblies, and salvage assemblies from disabled tanks. I can’t recall, but I think it was 16 bolts.
Here’s a Panther, PzKwV
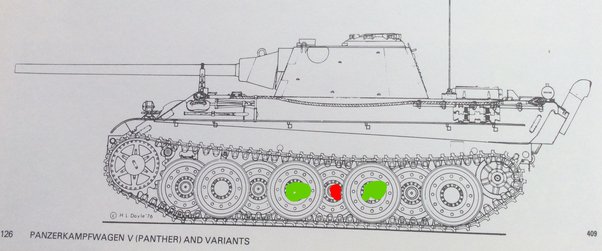
If the red road wheel goes bad, both green ones come off.
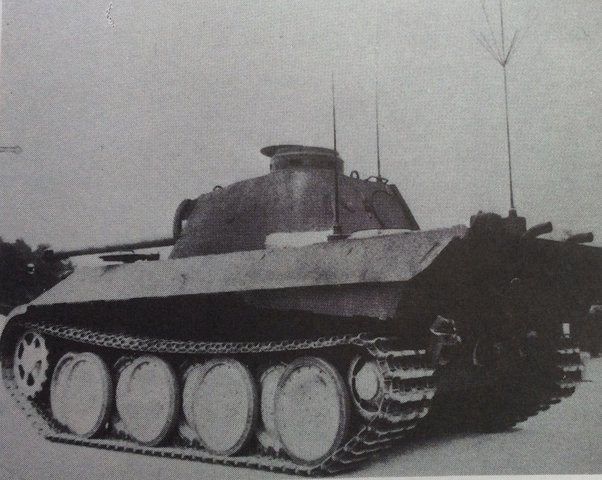
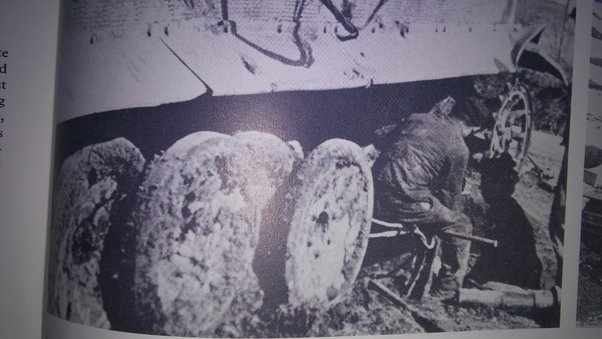
Here’s a Tiger I, PzKW VI.
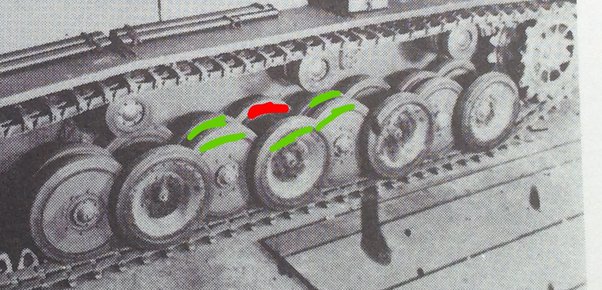
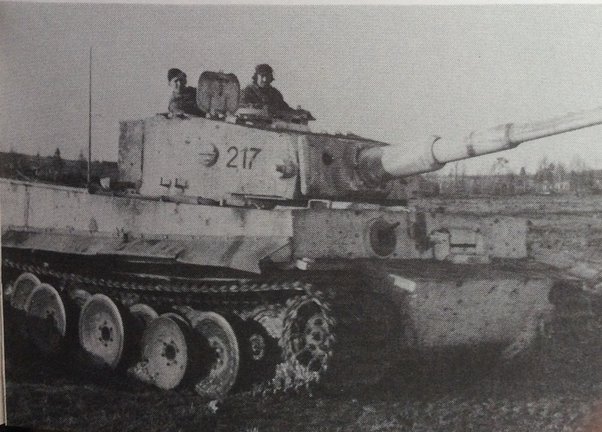
If the red road wheel goes bad, what do you think has to happen.
So I think when people say “over engineered”, they mean the Germans found the best technical answer for a given problem. But the best answer to solve an engineering problem does not produce the best vehicle for field use, because things break. Even without combat damage, things break. I know. Engineers will say a real engineer would take into account intended use. Which is why they stamp, their feet and foam at the mouth when you say “over-engineered”.
And because Hitler wanted the best tanks that could be built, that’s what he got. He forgot the ease of maintenance bit.
For a comprehensive look at all German weaponry of WW2, I recommend this, where you hear repeatedly, things like “29 of this type were built.” German War Files – YouTube
EDIT ONE: Another interesting point, tangential to this was how well equipped crews were to repair their own tanks. Thanks to Murphy Barrett for reminding me..
In 1939, the presence of cars in a society dictated acertain amount of mechanical “savvy”. Many people could (and did)work on their own vehicles, teens, as always, tinkered with them, and there were mechanics and garages proportionate to the need, that is, the number of cars present in that country.
In 1939:
There was 1 car for every 4.4 people in the US. In Italy, there was 1 car per 130 people. Great Britain, 1 per 32. Germany, 1 per 37.5, and France, 1 per 23.3.
In fact, my Dad was a mechanic at 18 before joining up. The point is, population that already had a lot of civilian mechanical expertise in peacetime, carried that in to war.
Source: “Dirty Little Secrets Of World War II” by James F. Dunnigan and Albert A. Nofi
Due to the plethora of comments that were either off point or so obscure as to be irrelevant, I have disabled comments for this answer. Thanks to those that provided useful or clarifying ones, including but not limited to Mr. Barrett.
All photos Courtesy of:
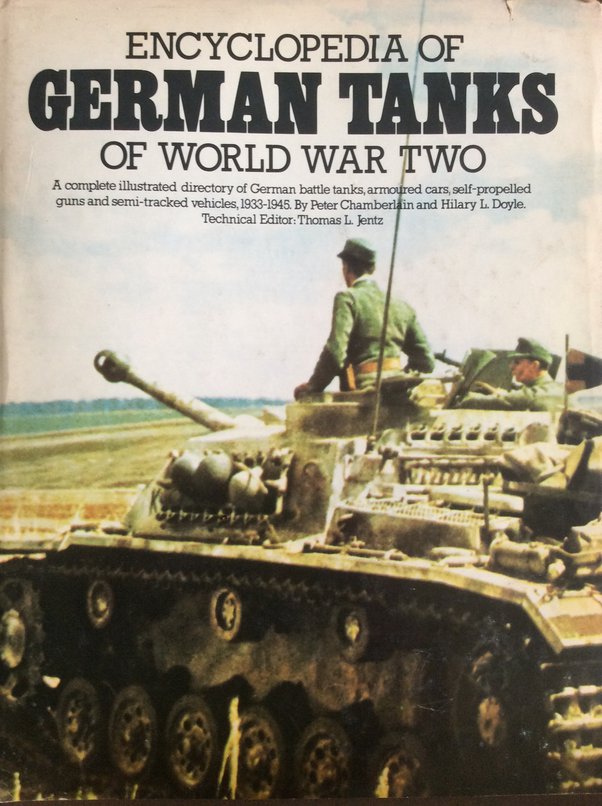
EDIT TWO: (2–26–1019)
This makes interesting reading.
It is an analysis of a piece of glacis armor from a Panther tank, performed at the Watertown Arsenal, in February 1945. It points out something that none of the generalizations ever cover, because they can’t.
Lack of skilled labor (???? improper quenching) and lack of raw materials (vanadium is substituted for molybdenum) results in armor far more brittle than what the design calls for, and all the analysis you read, everywhere, fails to contemplate.
As the war went on, the destruction of transportation, the conscription of skilled labor into the armed forces, and the shrinking size of the Reich (and so, it’s access to raw materials), the quality of armor, (and we can assume other manufacturing related issues) resulted in a degradation in German industrial performance and consistency.
The correspondence accompanying this sample is dated October 1944, 7 months before the end of the war, and we can presume, captured a month or more prior. The Panther had only been in use since February 1943, and was rushed through production and out into the field before it had gone through normal acceptance testing, and thus had a number of design/manufacturing issues. It wasn’t until mid 1944 that these had been resolved, but the Panther still only had a 54% availability
[1].
So these Panthers, supposedly defect free were likely the same as the ones the sample came from.